The effects of temperature accurate DHW on energy and its properties as a thermal disinfectant within a high volume/commercial laundry setting
In today’s world it is clear to see that implementing temperature precision and control in the specification andinstallation of hot water systems is vital. Whether that be for designing out issues before they emerge or combating them head on, it is a key consideration that is gaining more traction by the day. An important ability of hot water is that of thermal disinfection, especially in particular industries such as health & care home laundry. This can be seen within the Health & Safety Executive’s HSG (95)18 Hospital Laundry Arrangements for Used and Infected Linen which states “The washing process should have a disinfection cycle in which the temperature in the load is maintained at 65ºC (150ºF) for not less than 10 minutes or, preferably, at 71ºC (160ºF) for not less than 3 minutes”. In conjunction with this benefit, the ability to supply water accurately at hotter temperatures will save time and energy consumption as it would reduce or even possibly eliminate the time and power required to bring the water up to the required temperature.
Laundry practise, especially in the health and care home sectors, can generally act as one of the gateways to infection breakout - or one of the keys to preventing infection. This point is alluded to in a 2020 paper entitled “The role of textiles as fomites in the healthcare environment:a review of the infection control risk” (Owen, 2020). With causes ranging from incontinence to open wounds, clothes, towels, linen and other types of fabric may come into contact with all manner of bodily fluids, purely due to the nature of the industry and so it is imperative than when it comes to handling soiled laundry,not only is all contaminated linen managed and separated appropriately but thermal disinfection is properly implemented. In essence, thermal disinfection is the use of above average wash temperature for a set cycle time to ensure any potentially infectious microbes, such as blood-borne pathogens (HIV, Hepatitis) or Clostridium difficile, are killed. These bacteria, as well as the likes of Staphylococcus aureus - a well-known pathogen that if allowed to invade the skin deeply can cause a plethora of diseases, ranging from superficial skin infections that cause boils to more systematic issues like pneumonia and blood infections - can survive temperatures of over 50°C degrees and so using wash cycles that are not only hot enough but long enough to destroy the potentially infectious bacteria is critical for the wellbeing of the recipients of the laundered items. With this in mind it is important the washing process is tested and verified. One way of doing this is by using a swatch of fabric with a certain amount of the bacteria in question on it, placing it in the washing machine and going through a typical wash cycle. After the cycle, you would measure the bacteria left to see if it has been effective, which is conveyed by a microbial log reduction. This is a mathematical scale that displays how successful a product is at reducing pathogens – the greater the log reduction, the more effective the product is at killing bacteria. In this case you would look for at least a 5 log reduction. ‘Log’, short for logarithm, is a mathematical term for a power to which a number can be raised. For example, if using 10 as a given number, a Log 3 increase can be shown as 103 or 10 x 10 x 10 = 1,000. A log reduction takes the power in the opposite direction. For example, a log reduction of 1 is equivalent to a 10-fold reduction or, to put it another way, moving down one decimal place or a 90% reduction. In micro-biology, a colony forming unit (CFU) is a unit used to estimate the number of viable bacteria in a sample. The number of CFU’s present would be counted before and recounted after the cycle and the resultant difference would be declared as the log reduction. For example, if the number of CFU’s beforehand was found to be 10,000,000 (107) and the end result was 100 (102) then as it is 100,000 times smaller, that would be log reduction of 5 or 99.999%.
Temperature not only plays a key role in disinfection but also in saving energy. As mentioned before, the washing machines heat up the incoming water to the required temperature. This consumes energy andso the smaller the difference between the incoming and required temperature, the lower the consumption as it would take less time. In the realm of laundry, time dictates capacity. This means that the longer the cycle takes, the less loads you can wash in a set time period. This ultimately leads to investing in more machines. The reverse is also true in that you can reduce the amount of washing machines needed by reducing the total time of a wash cycle and the variable part that can be reduced is the time needed to heat up the water. For example, imagine a scenario where you had 2 loads to wash, a 90min window in which to do it in and each cycle took 60mins. You would need to have 2 machines. If the total cycle time could be reduced to 45mins, then 1 machine would suffice, not only saving consumption but cost as well.
Additionally, if the water heater connected to the machine is more efficient, this further reduces overall consumption. This next part of this paper will explore two of the mains ways to supply washing machines with hot water - instantaneous continuous flow water heaters piped directly into the washing machines and having the washing machines connected to conventional storage water heaters.
Storage tank options tends to be less efficient and consume more energy. Once you factor in costs of replacement, it is clear that a continuous flow heater is the more cost and energy efficient option as well as being better at reducing the carbon footprint. Due to their ability to modulate, continuous flow heaters only provide an output in response to the water flow and temperature demand. This means that depending on what is required, the KW rating can range anywhere from a given maximum output to a minimum. However, one of the most important features, and what makes continuous flow the preferred option for many applications, is the ability of some instantaneous water heater models to constantly provide temperature accurate hot water with a precision of up to ±1°C. Table 1 (previous page) shows us a comparative analysis between 2 continuous flow heaters and a storage tank water heater that are supplying a laundry. Based on a load requirement of 120L and a usage of 10 wash cycles per day, you can see that not only is the continuous flow more efficient but is also able to supply the required volume of water in half the time. It also doesn’t have to worry about replenishing storage or any standing losses. This results in a lower consumption, less carbon produced and money saved every year. Storage, at least in the form of a separate vessel, does have its placehowever. It provides a good option to meet peak demand when continuous flow heaters may not meet the requirements. In this case, the optimal setup would be a continuous flow connected to a buffer vessel. The system would regenerate during demand dips as usual and so this combination would allow for a virtually limitless maximum flow rate.
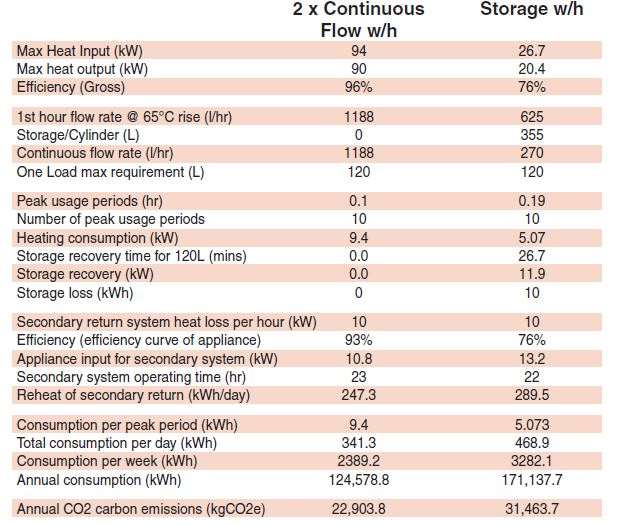
The benefits of temperature precise hot water are many and in a world where issues regarding hygiene,bacteria or emissions are being even more heavily scrutinised, water supplied by continuous flow water heaters are surely part of the solution. Some continuous water heaters have a proprietary capability that enables them to deliver temperature accurate hot water at temperatures ranging up to 85 degrees, securing best practice against the aforementioned HSE guidance as well as eliminating storage and pipework losses. Being able to reliably provide water at these temperatures not only serves to properly disinfect the items in question but gives you constant peace of mind. As mentioned before, these systems also have the ability to modulate, with turn down ratios of up to 13:1. For example, if a heater has a maximum output of 58.3kW, it can potentially modulate downto a minimum of 4.4kW. This huge difference results in a significant reduction in energy consumption and therefore emissions as it is not constantly operating at maximum power. With all this in mind, they are able to provide optimum performance and operational efficiency, some of which is displayed in Table 1 and Figure 1 above.
Bibliography
Owen, L. L. (2020). The role of textiles as fomites in the healthcare environment: a review of the infection control risk. PeerJ, 35.